Global Warming Prevention
The Kikkoman Group has set the goal of 50% reduction in CO2 emissions due to global warming by FY2030 in comparison to FY2018. To accomplish this goal, we carry out initiatives such as the utilization of renewable energy sources, process improvements, and introduction of energy-efficient facilities.
Utilization of Renewable Energy Sources
Renewable Energy-Derived Electricity
The Kikkoman Group has started shifting to "renewable energy sources" for electricity used in each department.
Facilities in Japan using 100% renewable energy-derived electricity (in order of transition-completed year):
2020 |
Kikkoman Noda Head Office, Saitama Kikkoman Company, Kikkoman General Hospital
|
---|---|
2021 |
Kikkoman Soyfoods Company (Gifu Plant), Kikkoman R&D Center, Kikkoman Foodtech Company (Nakanodai Plant) |
2022 |
Kikkoman Tokyo Head Office, Kikkoman Foods Products Company (Noda Factory), Kikkoman Foodtech Company (Main Plant, Edogawa Plant), Manns Wine Co., Ltd. (Katsunuma Winery, Komoro Winery), Kikkoman Biochemifa Company (Edogawa Plant, Kamogawa Plant), Hokkaido Kikkoman Company, Nagareyama Kikkoman Company, Kikkoman Soyfoods Company (Saitama Plant, Ibaraki Plant) |
2024 |
Kikkoman Kinki Office |
Facilities overseas using 100% renewable energy-derived electricity (in order of transition-completed year):
2021 |
Kikkoman Foods Europe B.V.
|
---|---|
2023 |
Kikkoman Foods, Inc. (Folsom Plant), JFC International Inc. (North America offices)* |
* Achieved 100% renewable energy-derived electricity by combining renewable energy certificates (RECs) with purchased electricity.
In fiscal 2025, renewable energy-derived electricity is expected to account for 75% of the total electricity used by the Kikkoman Group in both Japan and overseas.
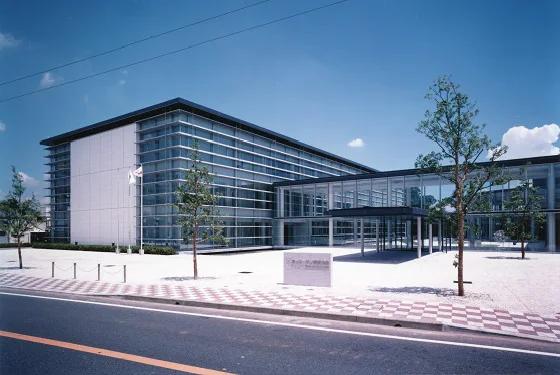
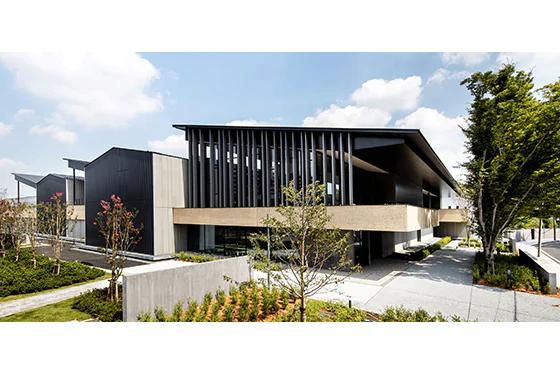
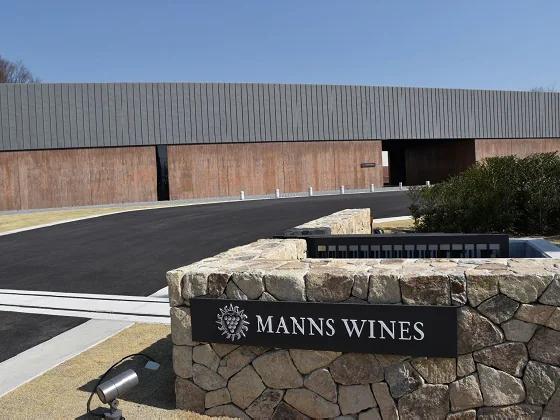
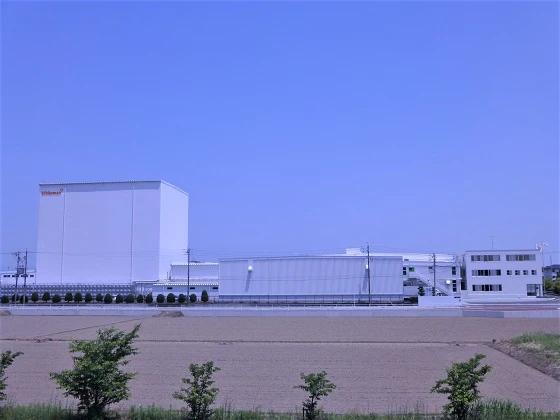
Kikkoman Soyfoods Co. (Gifu Plant)
Utilization of Carbon-Neutral LNG
In addition, gas use has been fully switched to Carbon Offset City Gas at Kikkoman Noda Head Office, Kikkoman R&D Center and Brewing Development Center, and partially switched to Carbon Offset City Gas at Kikkoman Foods Company (Takasago Factory) and Kikkoman Foodtech Company (Nishinippon Plant).
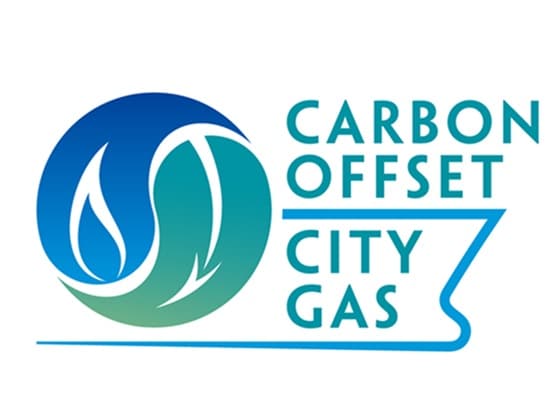
The Kikkoman Corporation is a member of the Carbon Offset City Gas Buyers Alliance.
PV Systems Installation
In an effort to reduce CO2 emissions, we have been installing PV (photovoltaic or solar panel) systems on our building roofs to generate a clean electricity source from sunlight (energy) for use in our operations.
* Installation completed at 5 locations as of July 2025
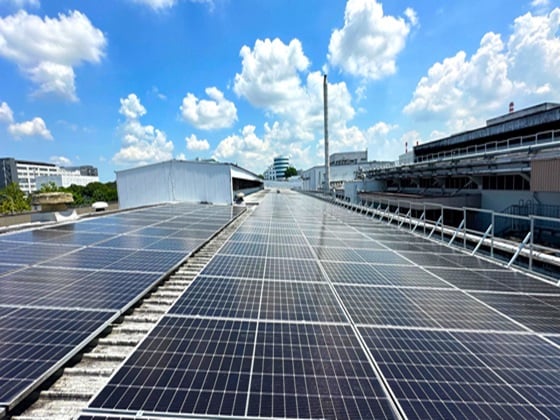
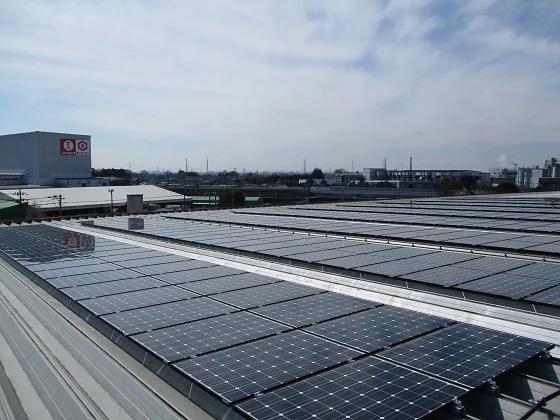
Kikkoman Foodtech Company, Head Office & Plant (Japan)
Production Department Initiatives
The Kikkoman Group's production departments assess production methods, facilities, and energy sources to reduce greenhouse gases.
Steam Reduction in Rotary Koji Making
Kikkoman Food Products’ Noda Factory previously used steam insulation to prevent condensation, which occurred when cold air entered the rotary koji making room through gaps due to deterioration of inside walls. We were able to discontinue the use of steam insulation by closing these gaps, which allow in cold air, as much as possible.
This measure resulted in a reduction of steam usage during the koji making process by approximately 20 percent and of CO2 emissions by 360 tons per year.
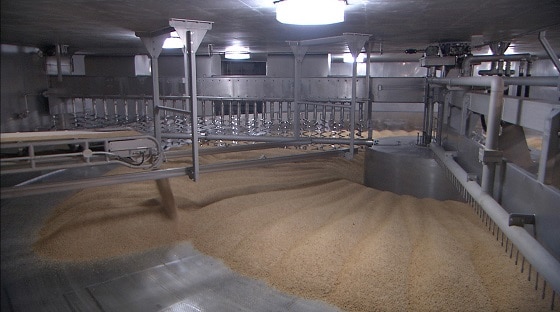
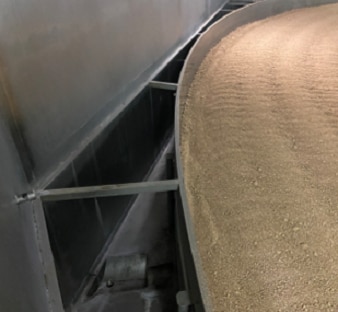
Freezer Replacement (March 2021) – 2 Units
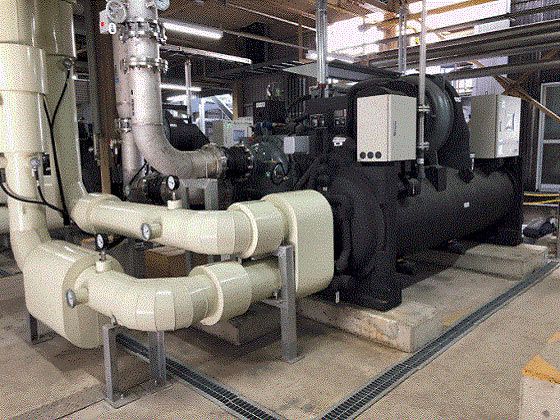
At the Kikkoman Foods Takasago Plant, we introduced new freezer units that monitor the temperature of chilled water inlets to maintain a stable temperature in the chilled water tank. This enables efficient continuous operation. As a result, we expect to reduce CO₂ emissions by approximately 600 to 800 tons annually.
Small Boiler Replacement (September 2021) – 4 out of 18 units
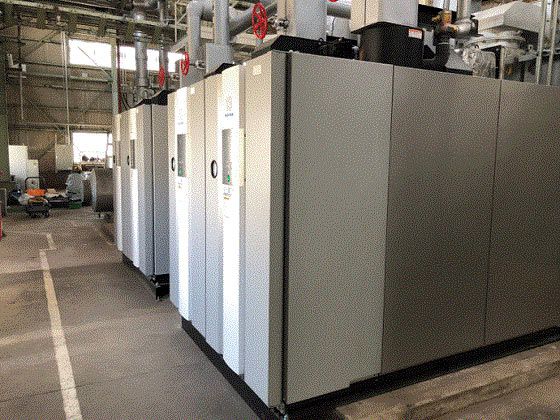
At the Kikkoman Foods Takasago Plant, we introduced small boiler units designed to efficiently recover and reuse waste heat from exhaust gases. Once all 18 units are replaced, we expect to reduce CO₂ emissions by approximately 200 tons annually.
Consolidation of Raw Ingredient Silos
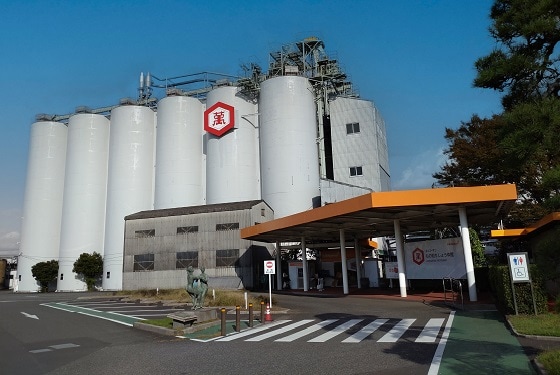
At Kikkoman Food Products Company (Noda Factory), by improving the on-site large silo for various purpose usage and consolidating raw ingredient storage, we discontinued the long-distance (appx. 300m or 984 ft) pneumatic conveyance system from an off-site large silo and decommissioned the large blower used for this system. This resulted in a reduction in energy used for the large blower equivalent to 94t-CO2 emissions annually.
Temperature Control Adjustment for Mirin Fermentation and Aging Tanks
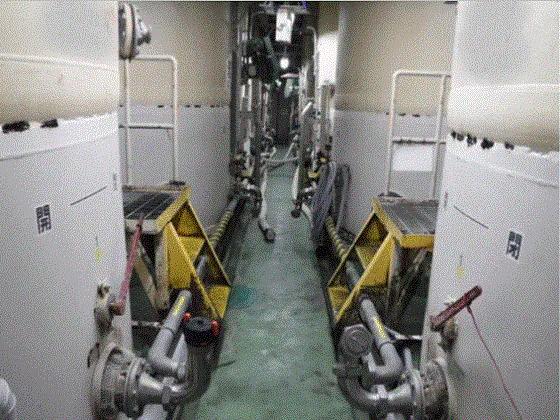
At Nagareyama Kikkoman Company, we succeeded in setting and controlling an appropriate temperature to process rice during the fermentation and aging (shikomi) process for moromi used to produce mirin, and establishing an agitation method to shorten the aging time. This reduced steam used to heat the fermentation and aging tank in summer. From this, we expect a 25.8-t reduction in CO2 emissions, previously resulting from steam generation, annually.
Recovering Air Compressor Waste Heat
From September 2023 at KFE (Kikkoman Foods Europe B.V.), our soy sauce production site in the Netherlands, we have been recovering waste heat from air compressors and reusing it for the heaters in some shikomi (fermentation and aging) tank rooms. This resulted in a decrease of about 36.5 t-CO2 of natural gas in comparison to the period between September and March of the previous year. We plan to deploy the same initiative in other facilities with high heat waste to further reduce energy use and CO2 emissions.
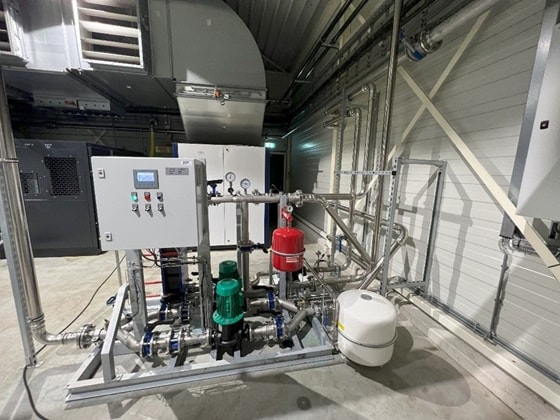
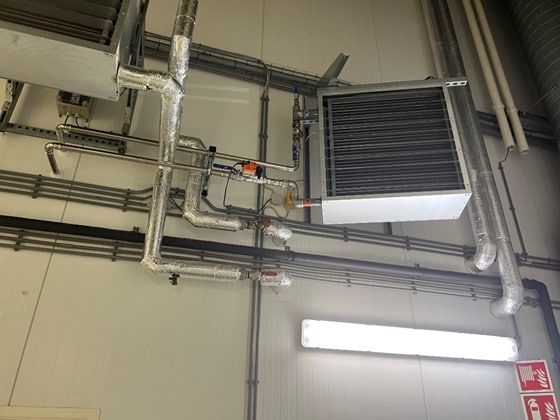
Switchover from Watertube Boilers to Once-Through Boilers
At the Hokkaido Kikkoman facility, a 10-ton watertube boiler was previously used to generate steam for various production processes. Among these, raw ingredient processing accounts for approximately 20% of the plant’s total steam usage. In February 2022, the facility transitioned to five 2.5-ton once-through boilers, which are highly efficient and capable of adjusting combustion based on load. As a result, CO₂ emissions from raw ingredient processing were reduced by 26% compared to FY2021, prior to the switchover.

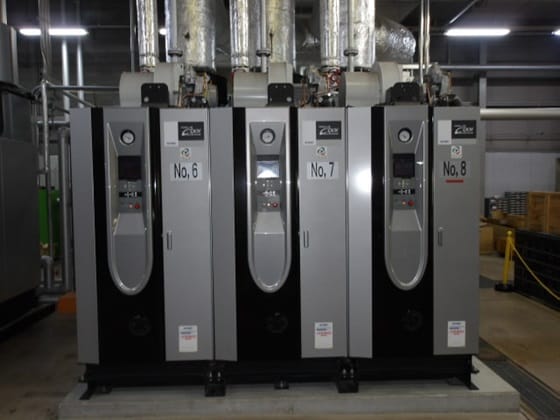
Initiatives Across Logistics Departments
The Kikkoman Group pays careful attention to CO2 emissions from our logistics departments (consolidated subsidiaries including Sobu Logistics Co., Ltd.) and is carrying out efforts for reduction.
Streamlined Shipping
By reviewing basic criteria for shipment lots and delivery destinations, we increased the number of products that could be shipped to each customer in a single delivery, resulting in improved shipping efficiency.
Exterior Package Review for Increased Load Factor
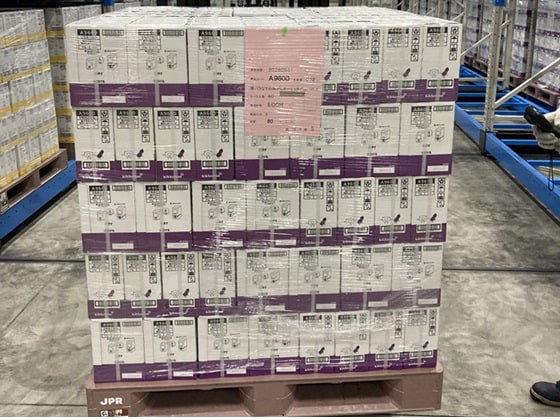
By reviewing the exterior size of our products, we are working to improve vehicle loading efficiency by increasing the number of loading cases per pallet.
Joint Shipping
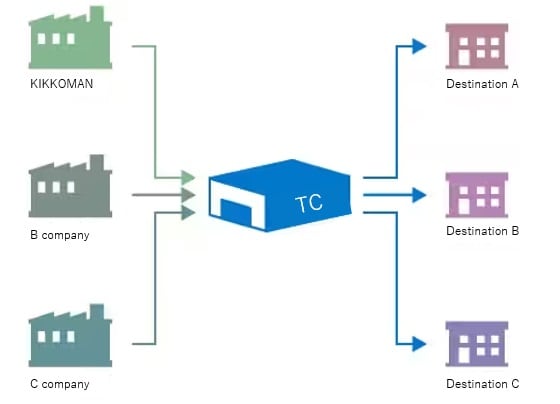
We consolidate food manufacturers’ products, including those of other companies, at our Transfer Centers (TC), and then deliver these to business partners, throughout Japan together with other manufacturers’ products. In this way, we contribute to reducing environmental impact by improving shipping efficiency.
Modal Shift
Kikkoman has been certified as an “Eco Rail Mark Company” by the Japan Railway Freight Association. The “Eco Rail Mark” is a mark that may be used by companies and products officially recognized for proactive use of railway freight transport on their packages and catalogs. We are contributing to reducing CO2 emissions and preserving the global environment by promoting a modal shift from truck to railway and maritime transport for mid- to long-range logistics.
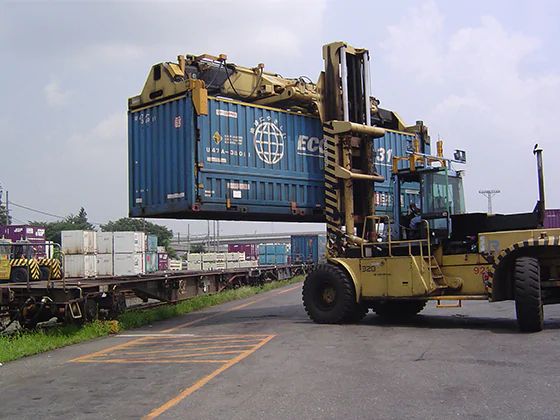
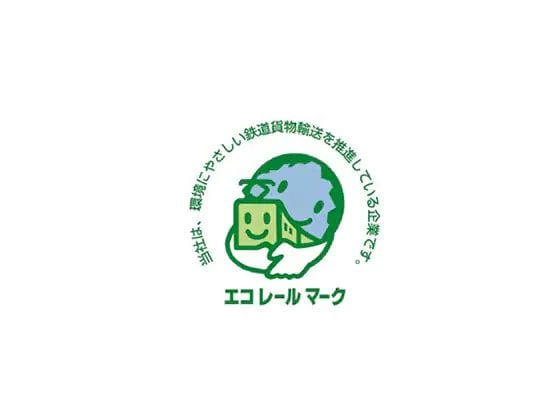
Low Pollution Vehicles & Idling Stop Systems
As an initiative for environmental conservation, Sobu Logistics Co., Ltd. is proactively introducing low pollution vehicles.
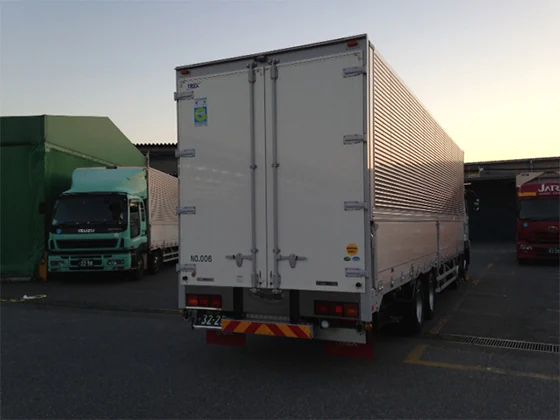
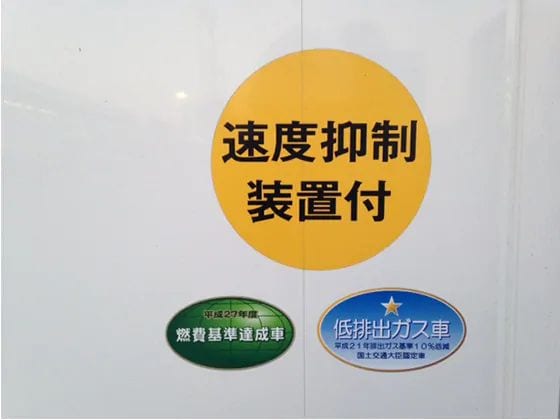
We are committed to achieving green transport by introducing trucks equipped with idling stop coolers powered by on-board batteries for one to two hours, producing zero emissions, as well as idling stop heaters that use 1/10th of regular diesel fuel amounts.
Moreover, we are striving to further reduce CO2 emissions by raising the level of awareness within our transport facilities, such as by using idling stop systems, restricting speed, and conserving energy and resources. In addition, we aim to further reduce CO2 emissions by introducing fuel-efficient, low-emission trucks and fully promoting green transport.
Office Space Initiatives
In Kikkoman Group’s offices, we are pursuing a wide range of initiatives. These include controlling room temperatures in summer (28°C) and winter (20°C), encouraging employees to wear lightweight clothes in summer, reducing the use of lighting, turning off lights when not in use, strictly controlling the use of OA equipment, encouraging the use of video conferencing system, practicing ecological driving, and introducing fuel-efficient or hybrid cars.
The Kikkoman Noda Head Office building in Noda City, Chiba Prefecture was designed to be an "environmentally sustainable office." In keeping with the goal of being in harmony with the natural environment and reducing environmental impact, various advanced technologies have been employed.
The building has been highly acclaimed by experts, receiving the New Office Promotion Award of the Nikkei New Office Award Program and the Architectural Culture Award of Chiba Prefecture in 2001, the Examination Committee Encouragement Prize of the 9th Environmental and Energy Saving Architecture Award in 2002, the 4th Sustainable Architecture Award by the Japan Institute of Architects (JIA) in 2003, and the Special Award "Ten-Year Award" of the Society of Heating, Air-conditioning and Sanitary Engineers of Japan (SHASE) in 2011.
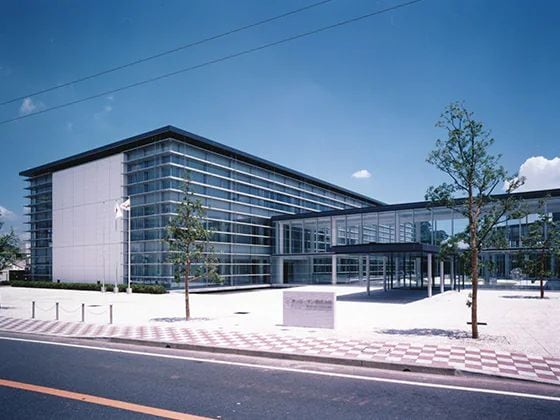
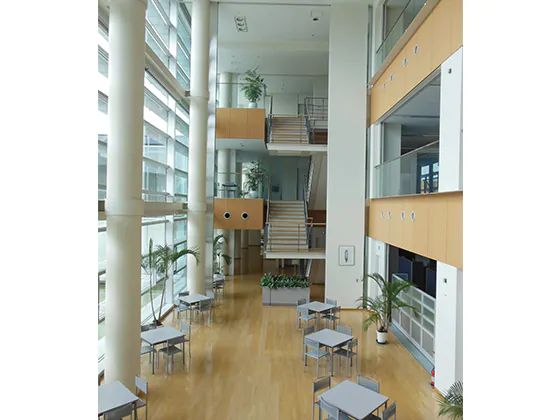
The Noda Head Office compound consists of an Office Building (North Building) and a Conference Room Building (South Building).
In the rectangular-shaped Office Building stretching from east to west, office rooms are arranged on the north side that is less affected by sunlight to ensure stable work environments. On the south side is an atrium-style entrance hall. In addition, we installed large windows to fully utilize natural sunlight and breeze. Other equipment aimed at energy reduction were also introduced for lighting and air-conditioning, including the luminance control system using a daylight sensor, the horizontal external louvers to control amount of sunlight in rooms, and double-glass air flow to enhance insulation.
In addition, the building has been switching to LED lighting to further promote energy savings.
Introduction of Electric Vehicles
One passenger car at the Kikkoman R&D Center and two passenger cars, and one small utility van at the Kikkoman Noda Head Office have been switched to electric vehicles, and on-site charging stations have been installed. We will consider the further introduction of electric vehicles, taking into account the availability of external charging infrastructure.
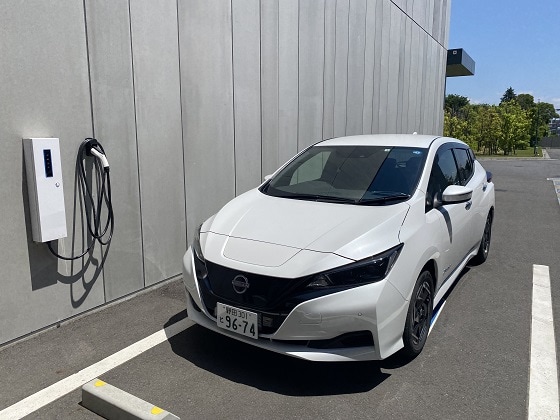
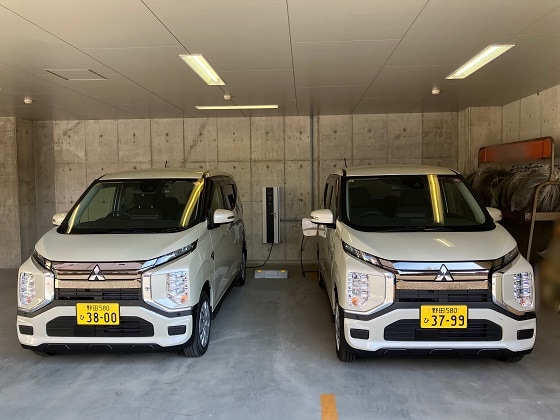
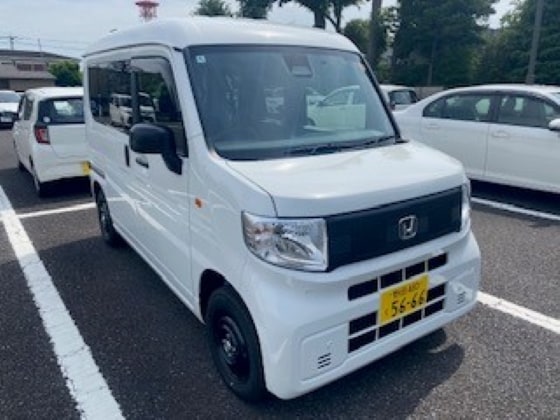
Kikkoman General Hospital
The Kikkoman Group has been managing Kikkoman General Hospital as part of contributions to the local community in Noda City, Chiba Prefecture, the birthplace of Kikkoman.
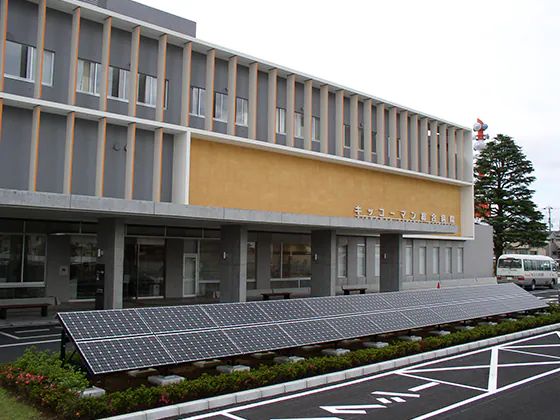
(Solar panels in front of the building)
With a base-isolated structure, the new building constructed in 2012 is designed to maintain functional integrity even in times of natural disaster. Additionally, eco-friendly measures such as enabling full utilization of natural lighting, placement of solar panels at the entrance for power generation, efficient use of well water, and implementation of energy saving equipment and instruments have been incorporated.
The Kikkoman Group will continue initiatives to further reduce CO2 emissions.